ABB flowmeter saves losses for top American universities to improve efficiency and energy saving
/div> & nbsp;& nbsp;& nbsp; The steam supply station of Virginia Commonwealth University, located in the east of the United States, uses ABB's new flowmeter, which reduces the annual loss caused by steam metering error from 16% to 5%, by more than 2 / 3, equivalent to US $1275000 in cash.
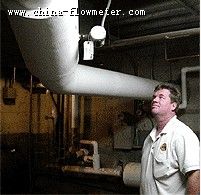
Staff check ABB new vortex flowmeter
The University of Virginia federal steam station supplies steam to nearly 60 buildings in the surrounding area, including hospitals, apartments and museums. In the financial quarter of 2006-07, the steam supply station produced 19000 tons of steam. However, when collecting fees from users, due to the large error in the flowmeter used to count the steam consumption of users, the supply station only recovered the money equivalent to 16000 tons of steam. As for the remaining 3000 tons of steam, the supply station had to "pay" out of its own pocket.
After detailed investigation, the steam supply station decided to listen to the advice of an authoritative flow control expert and use ABB's new swirl flow meter to replace the old one. Virginia Commonwealth University has a lot of old buildings. These buildings have short internal steam pipelines, which makes it difficult for traditional flowmeters which need long and straight pipelines to carry out measurement, resulting in large errors; ABB vortex flowmeter only needs a very short straight pipe to complete the work accurately, which is not affected by the short pipeline.
Vortex flowmeter is a member of ABB liquid, gas and steam flow equipment family. ABB vortex flowmeter has high accuracy and built-in temperature sensor, which can automatically measure and display the reading of steam consumption. These readings can be read manually or transmitted to the automatic control system of the building in real time.
At present, about 40 buildings have been replaced with abb vortex flowmeter, and the installation of the other 20 buildings is in progress. After the completion of these works, the steam supply station is expected to receive 127 million yuan per year$25000 in "extra" revenue.
It is particularly worth mentioning that the new steam flowmeter not only "makes money", but also arouses the attention of efficiency and energy saving in the whole campus. As the steam measurement has become more accurate, the slightest waste can be converted into the figures on the bill, so all departments of the school have begun to seriously study how to save steam and achieve efficiency and energy saving, which objectively reduces the overall carbon emissions of the school.
ABB automation shows its magic power, drinking water flows from sand dunes
When it comes to tap water, many people will immediately think of the huge workshops and dazzling chemicals of the traditional waterworks. Such a production mode needs to change the face of the land. At the same time, it involves the application of a large number of chemicals, which will more or less have a certain impact on the environment. Is there any way to make tap water more eco-friendly? Dunea, a leading water treatment company in the Netherlands, did. Through its unique eco-friendly water purification technology, dunea uses sand dunes to purify river water into drinking water that can meet the needs of 1.2 million people. ABB automation technology plays a key role in the whole drinking water production and distribution process.

Dune water purification facilities in dunea
Dunea is one of the largest water treatment companies in the Netherlands, responsible for supplying drinking water to 1.2 million people in the Hague and surrounding areas. Its environment-friendly sand dune water purification technology is unique in the world. First, the river water is pumped up, the sediment is filtered out, and then transported to the sand dunes by the sea; Then, the river slowly penetrates through the sand dunes, and in the process, the sand purifies the water. After about two months, the river can "cross" the sand dunes, collect it, filter and soften it again, and then "transform" into drinking water, which is finally transported to thousands of households through pipelines.
Dunea has five such facilities. In order to control the production process, in the past, dunea installed an independent process automation system for each site. Each system needs a separate control room, a separate controller, a separate software and hardware, and a separate operation strategy. Although this operation mode ensures the operation of each set of production facilities, it also takes up a lot of manpower and materials, and it is difficult to optimize the production at the whole company level, so the overall efficiency is not satisfactory. Today, with the help of ABB's award-winning extended automation system 800xA, this cumbersome and inefficient control has become history.
With excellent technology, 800xA can integrate dunea's original five multi process control systems into a control system covering the whole company. With this integrated control system, all kinds of production activities of the whole company are under the control of a central control room at any time, whether it is to retrieve the data and images of each production site, or to consult the operation manual, or to send instructions, or... Instead of the "big driver" of the original five control systems. From five systems to one system, dunea has realized the standardization and integration of process control. The benefits of this improvement are huge. It greatly improves the efficiency of the company, reduces the operation and labor costs, improves the reliability of the production process, and further ensures that residents can obtain stable, safe and high-quality drinking water.
< br > the partnership between abb and dunea began in the 1980s. As the scalability and flexibility of ABB control system are in line with dunea's design concept, and the cost is very competitive, dunea has been a loyal user of ABB products and systems since then.
New capacity of Arctic copper mine
High efficiency is a matter of life and death for the aitik copper mine in northern Sweden. The metal content of the soil there is only 0.3%, so only highly automated mining processes can guarantee profitability.
A three-year project costs 7The $390 million modernisation of ABB's new power and automation solutions has helped the operator of the copper mine, boriden, double its capacity and increase its workforce by only 10%. On August 31, 2010, the king of Sweden personally unveiled the upgraded copper mine.
Aitik copper mine is located in Lapland, Sweden, in the Arctic circle. As early as the 1930s, people had found that there was copper ore, but it was not until 1968 that people began to develop this copper mine after they had the profitable mining technology. In 2006, with the surge in copper demand, Boliden decided to make the largest investment in its history to increase production capacity.
Aitik is Sweden's largest mine and an efficiency benchmark for the global mining industry. After upgrading, Boliden can mine ore buried deeper underground, thus extending the production life of aitik copper mine to 2029.
Aitik mine can produce up to 100000 tons of ore per day. At the mining site, giant excavators strip the ore from the rock and load it into transport trucks. The wheels of these trucks are more than one floor high and carry more than 200 tons. They are responsible for transporting ore to the crusher. In the crusher, the ore is broken down into stones about 30 cm in diameter, which are then transported by conveyor belt to the storage site for stacking.
When the ore arrives at the storage site, their journey is not over. Through another conveyor belt, the ore is transported to a concentrator several kilometers away, which separates valuable minerals from worthless waste.
ABB played a key role in the whole upgrade project, providing a total of 84 million US dollars worth of products and systems for the power and automation facilities related to the project.
About 650 ABB energy efficient motors (quite a few of which are equipped with frequency converters) are used to drive conveyor belts, pulverizers, water pumps, fans and process equipment in order to minimize energy consumption and achieve the best possible process efficiency.
Inside the concentrator, driven by two of ABB's most powerful gearless mill drives, two mills grind ore into sand to extract copper from the middle. The power of each set of ABB gearless mill transmission equipment is up to 225 MW, equivalent to the output power of 280 medium-sized cars. The powerful power enables each mill to process up to 2200 tons of ore per hour.
The full set of on-site process system C of the mine, including concentrator, conveyor belt control system and pump station C, is controlled by ABB's expanded automation system 800xA. After many comparisons and tests, Boliden company has selected 800xA system as the process automation platform of the whole group a few years ago. An ABB gas insulated substation continuously inputs power from the power grid to aitik copper mine, and its own land occupation and electrical loss are also controlled at the lowest level. In addition, abb has also provided a set of harmonic and power factor correction filtering system, which can ensure that the copper mine will not disturb the power grid when using the high-power gearless mill, and will not receive fines from the power supply department.
In addition, the power input to the mine is also efficiently and reliably distributed to each electric field by ABB low-voltage switch.
ABB takes industrial productivity to a new level
Lohja limestone treatment plant, an energy intensive enterprise in Finland, with the help of ABB industrial facilities process control and optimization solution expert optimizer, which won the global industrial award, has increased industrial productivity by 9%, bringing huge profits to the plant.
Expert optimizer has successfully improved the productivity and energy efficiency of more than 200 production facilities around the world. In 2008, expert optimizer won the global fuels Award for 'most innovative technology for electrical energy efficiency'.
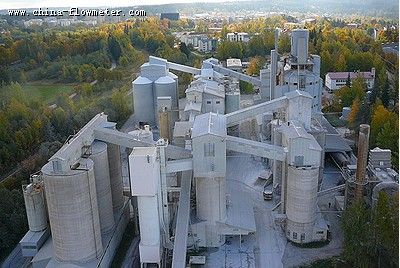
Production facilities with expert optimizer installed
Expert optimizer was originally developed for the cement industry, but now it has been applied to all process industries. Expert optimizer can coordinate the best operation parameters of all aspects of the process, and quickly find any deviation. Once deviations are found, expert optimizer can stabilize and re optimize the process. In addition, expert optimizer has the ability to calculate the optimal production schedule for the whole plant. In general, expert optimizer can increase productivity by 3% - 10%.
< br > ABB has been responsible for the maintenance of the whole production site in lohja since 2006, which is part of the full responsibility performance service contract signed by ABB and lohjia limestone treatment plant. Under the contract, abb will help the plant, one of the largest limestone treatment facilities in northern Europe, increase productivity and reduce maintenance costs.
With its world leading technical strength in power, automation and cement industries, abb uses expert optimizer to solve the production and energy consumption problems of C lime kiln, the core of lime manufacturing process.
Before the application of expert optimizer, it is difficult to determine the optimal operation state of the process because several different kinds of feed materials are loaded into the lime kiln at the same time. And expert optimizer can find the best operation state of each feed, so as to determine which state the lime kiln can exchange the maximum output with the minimum energy consumption. In the end, factory productivity increased by 9%.
In a typical full responsibility performance service contract, abb and its customers jointly determine and achieve the goals of maintenance cost, plant utilization, equipment reliability, energy efficiency and safety. At present, abb has signed more than 150 full responsibility performance service agreements with customers in petrochemical, papermaking, oil and gas exploration, steel and consumer goods and other fields all over the world.
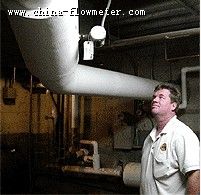
Staff check ABB new vortex flowmeter
The University of Virginia federal steam station supplies steam to nearly 60 buildings in the surrounding area, including hospitals, apartments and museums. In the financial quarter of 2006-07, the steam supply station produced 19000 tons of steam. However, when collecting fees from users, due to the large error in the flowmeter used to count the steam consumption of users, the supply station only recovered the money equivalent to 16000 tons of steam. As for the remaining 3000 tons of steam, the supply station had to "pay" out of its own pocket.
After detailed investigation, the steam supply station decided to listen to the advice of an authoritative flow control expert and use ABB's new swirl flow meter to replace the old one. Virginia Commonwealth University has a lot of old buildings. These buildings have short internal steam pipelines, which makes it difficult for traditional flowmeters which need long and straight pipelines to carry out measurement, resulting in large errors; ABB vortex flowmeter only needs a very short straight pipe to complete the work accurately, which is not affected by the short pipeline.
Vortex flowmeter is a member of ABB liquid, gas and steam flow equipment family. ABB vortex flowmeter has high accuracy and built-in temperature sensor, which can automatically measure and display the reading of steam consumption. These readings can be read manually or transmitted to the automatic control system of the building in real time.
At present, about 40 buildings have been replaced with abb vortex flowmeter, and the installation of the other 20 buildings is in progress. After the completion of these works, the steam supply station is expected to receive 127 million yuan per year$25000 in "extra" revenue.
It is particularly worth mentioning that the new steam flowmeter not only "makes money", but also arouses the attention of efficiency and energy saving in the whole campus. As the steam measurement has become more accurate, the slightest waste can be converted into the figures on the bill, so all departments of the school have begun to seriously study how to save steam and achieve efficiency and energy saving, which objectively reduces the overall carbon emissions of the school.
ABB automation shows its magic power, drinking water flows from sand dunes
When it comes to tap water, many people will immediately think of the huge workshops and dazzling chemicals of the traditional waterworks. Such a production mode needs to change the face of the land. At the same time, it involves the application of a large number of chemicals, which will more or less have a certain impact on the environment. Is there any way to make tap water more eco-friendly? Dunea, a leading water treatment company in the Netherlands, did. Through its unique eco-friendly water purification technology, dunea uses sand dunes to purify river water into drinking water that can meet the needs of 1.2 million people. ABB automation technology plays a key role in the whole drinking water production and distribution process.

Dune water purification facilities in dunea
Dunea is one of the largest water treatment companies in the Netherlands, responsible for supplying drinking water to 1.2 million people in the Hague and surrounding areas. Its environment-friendly sand dune water purification technology is unique in the world. First, the river water is pumped up, the sediment is filtered out, and then transported to the sand dunes by the sea; Then, the river slowly penetrates through the sand dunes, and in the process, the sand purifies the water. After about two months, the river can "cross" the sand dunes, collect it, filter and soften it again, and then "transform" into drinking water, which is finally transported to thousands of households through pipelines.
Dunea has five such facilities. In order to control the production process, in the past, dunea installed an independent process automation system for each site. Each system needs a separate control room, a separate controller, a separate software and hardware, and a separate operation strategy. Although this operation mode ensures the operation of each set of production facilities, it also takes up a lot of manpower and materials, and it is difficult to optimize the production at the whole company level, so the overall efficiency is not satisfactory. Today, with the help of ABB's award-winning extended automation system 800xA, this cumbersome and inefficient control has become history.
With excellent technology, 800xA can integrate dunea's original five multi process control systems into a control system covering the whole company. With this integrated control system, all kinds of production activities of the whole company are under the control of a central control room at any time, whether it is to retrieve the data and images of each production site, or to consult the operation manual, or to send instructions, or... Instead of the "big driver" of the original five control systems. From five systems to one system, dunea has realized the standardization and integration of process control. The benefits of this improvement are huge. It greatly improves the efficiency of the company, reduces the operation and labor costs, improves the reliability of the production process, and further ensures that residents can obtain stable, safe and high-quality drinking water.
< br > the partnership between abb and dunea began in the 1980s. As the scalability and flexibility of ABB control system are in line with dunea's design concept, and the cost is very competitive, dunea has been a loyal user of ABB products and systems since then.
New capacity of Arctic copper mine
High efficiency is a matter of life and death for the aitik copper mine in northern Sweden. The metal content of the soil there is only 0.3%, so only highly automated mining processes can guarantee profitability.
A three-year project costs 7The $390 million modernisation of ABB's new power and automation solutions has helped the operator of the copper mine, boriden, double its capacity and increase its workforce by only 10%. On August 31, 2010, the king of Sweden personally unveiled the upgraded copper mine.
Aitik copper mine is located in Lapland, Sweden, in the Arctic circle. As early as the 1930s, people had found that there was copper ore, but it was not until 1968 that people began to develop this copper mine after they had the profitable mining technology. In 2006, with the surge in copper demand, Boliden decided to make the largest investment in its history to increase production capacity.
Aitik is Sweden's largest mine and an efficiency benchmark for the global mining industry. After upgrading, Boliden can mine ore buried deeper underground, thus extending the production life of aitik copper mine to 2029.
Aitik mine can produce up to 100000 tons of ore per day. At the mining site, giant excavators strip the ore from the rock and load it into transport trucks. The wheels of these trucks are more than one floor high and carry more than 200 tons. They are responsible for transporting ore to the crusher. In the crusher, the ore is broken down into stones about 30 cm in diameter, which are then transported by conveyor belt to the storage site for stacking.
When the ore arrives at the storage site, their journey is not over. Through another conveyor belt, the ore is transported to a concentrator several kilometers away, which separates valuable minerals from worthless waste.
ABB played a key role in the whole upgrade project, providing a total of 84 million US dollars worth of products and systems for the power and automation facilities related to the project.
About 650 ABB energy efficient motors (quite a few of which are equipped with frequency converters) are used to drive conveyor belts, pulverizers, water pumps, fans and process equipment in order to minimize energy consumption and achieve the best possible process efficiency.
Inside the concentrator, driven by two of ABB's most powerful gearless mill drives, two mills grind ore into sand to extract copper from the middle. The power of each set of ABB gearless mill transmission equipment is up to 225 MW, equivalent to the output power of 280 medium-sized cars. The powerful power enables each mill to process up to 2200 tons of ore per hour.
The full set of on-site process system C of the mine, including concentrator, conveyor belt control system and pump station C, is controlled by ABB's expanded automation system 800xA. After many comparisons and tests, Boliden company has selected 800xA system as the process automation platform of the whole group a few years ago. An ABB gas insulated substation continuously inputs power from the power grid to aitik copper mine, and its own land occupation and electrical loss are also controlled at the lowest level. In addition, abb has also provided a set of harmonic and power factor correction filtering system, which can ensure that the copper mine will not disturb the power grid when using the high-power gearless mill, and will not receive fines from the power supply department.
In addition, the power input to the mine is also efficiently and reliably distributed to each electric field by ABB low-voltage switch.
ABB takes industrial productivity to a new level
Lohja limestone treatment plant, an energy intensive enterprise in Finland, with the help of ABB industrial facilities process control and optimization solution expert optimizer, which won the global industrial award, has increased industrial productivity by 9%, bringing huge profits to the plant.
Expert optimizer has successfully improved the productivity and energy efficiency of more than 200 production facilities around the world. In 2008, expert optimizer won the global fuels Award for 'most innovative technology for electrical energy efficiency'.
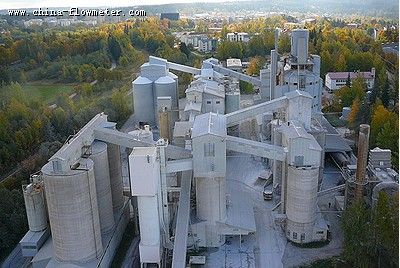
Production facilities with expert optimizer installed
Expert optimizer was originally developed for the cement industry, but now it has been applied to all process industries. Expert optimizer can coordinate the best operation parameters of all aspects of the process, and quickly find any deviation. Once deviations are found, expert optimizer can stabilize and re optimize the process. In addition, expert optimizer has the ability to calculate the optimal production schedule for the whole plant. In general, expert optimizer can increase productivity by 3% - 10%.
< br > ABB has been responsible for the maintenance of the whole production site in lohja since 2006, which is part of the full responsibility performance service contract signed by ABB and lohjia limestone treatment plant. Under the contract, abb will help the plant, one of the largest limestone treatment facilities in northern Europe, increase productivity and reduce maintenance costs.
With its world leading technical strength in power, automation and cement industries, abb uses expert optimizer to solve the production and energy consumption problems of C lime kiln, the core of lime manufacturing process.
Before the application of expert optimizer, it is difficult to determine the optimal operation state of the process because several different kinds of feed materials are loaded into the lime kiln at the same time. And expert optimizer can find the best operation state of each feed, so as to determine which state the lime kiln can exchange the maximum output with the minimum energy consumption. In the end, factory productivity increased by 9%.
In a typical full responsibility performance service contract, abb and its customers jointly determine and achieve the goals of maintenance cost, plant utilization, equipment reliability, energy efficiency and safety. At present, abb has signed more than 150 full responsibility performance service agreements with customers in petrochemical, papermaking, oil and gas exploration, steel and consumer goods and other fields all over the world.